On November 4th, Harbin Engineering University, Zhejiang University, Beihang University, Harvard University, the Institute of Deep-Sea Science and Engineering of the Chinese Academy of Sciences, and other institutions jointly published a forward-looking article in the internationally renowned journal《Nature Communications》: "Bioinspired soft robots for deep-sea exploration." The first affiliation of the paper is the Qingdao Innovation and Development Base of Harbin Engineering University. Professor Guorui Li from Harbin Engineering University is the first author and a corresponding author of the paper. Professor Tiefeng Li from Zhejiang University is a corresponding author. Professor Aman Zhang from Harbin Engineering University and others are co-authors of the paper.
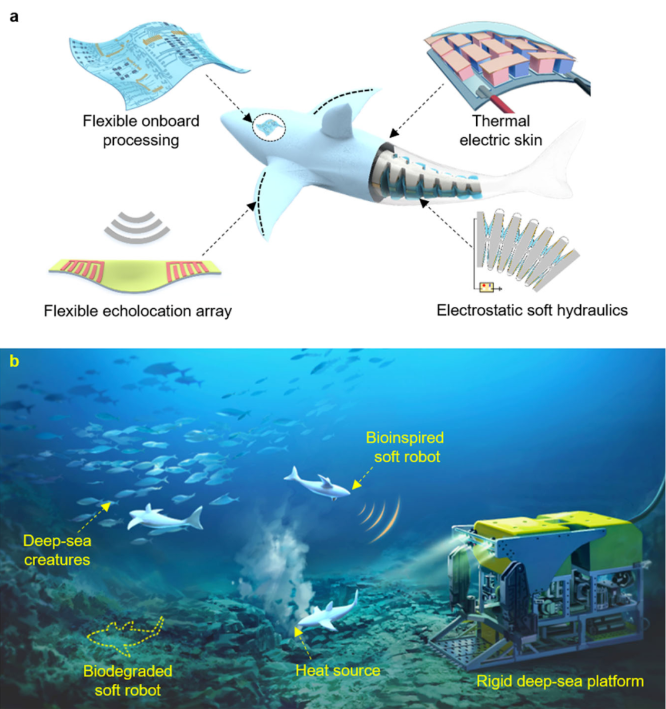
A prospective design and application scenario schematic for
future deep-sea soft robots.
This article, based on previous representative research, proposes a design theory and application methods for deep-sea soft robot systems from a biomimetic perspective. It is expected to advance the research progress of deep-sea soft intelligent systems, not only providing new solutions for special equipment operations in the deep sea, but also contributing to the cutting-edge research of deep-sea biomimetic intelligent systems.
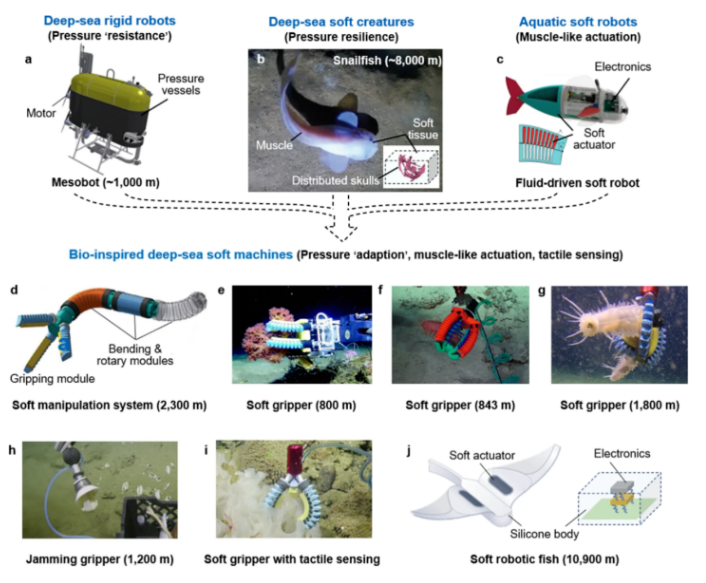
The development chart of deep-sea soft robots
Deep-sea robots, as an important technical means of current deep-sea exploration, play a significant role in the detection of seabed resources and extreme rescue operations. However, due to the extremely high hydrostatic pressure in the deep sea, the electromechanical components carried by the robots need to be protected by pressure-resistant housings or pressure compensation systems, which greatly limits the miniaturization, mobility, and cost-effectiveness of deep-sea robots and intelligent equipment.
Deep-sea creatures, due to their unique physiological structures, exhibit good adaptability to extreme environments, which provides abundant design inspiration for the research of new concepts in deep-sea equipment. As a cutting-edge branch in the field of underwater equipment, soft underwater robots take soft-bodied organisms as their biomimetic prototypes. Structurally, they are composed of highly flexible elastic materials; functionally, they use smart soft materials to replace motors or sensors to provide muscle-like actuation or perception. With their unique advantages of strong adaptability, high compliance, and self-sensing, soft robots have shown great potential in applications in the deep-sea field.
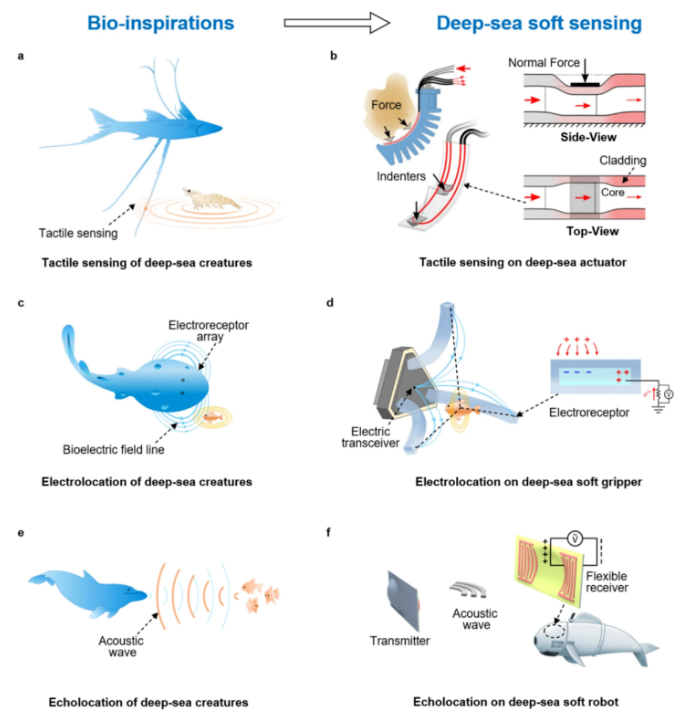
Soft sensors inspired by deep-sea creatures
This article discusses the actuation, sensing, and pressure self-adaptation design methods for deep-sea soft robots, providing a forward-looking perspective on propulsion, actuation, information perception, and mechanical design for deep-sea soft robots. In the future, deep-sea soft robots will integrate technologies such as flexible circuits, soft actuators, flexible sensors, and energy regeneration. Flexible circuit technology makes it possible to distribute the robot's internal pressure-resistant structures in a fragmented manner, thin-film acoustic sensors can achieve intelligent transmission of arrayed signals, and integrated deep-sea energy regeneration technology can provide feasibility for soft robots to stay and operate in the deep sea for extended periods.
"Conventional deep-sea equipment requires pressure-resistant housings for protection and is very expensive. As a disruptive technology, the cost of future deep-sea soft biomimetic robots can be significantly reduced. For example, through deep-sea soft robotic arms, samples and organisms can be collected without damage. Also, through deep-sea soft robotic fish, low-disturbance integration into deep-sea biological communities can be achieved for in situ detection, and biodegradable materials can be used to protect the original deep-sea ecosystem. In the future, a common deep-sea exploration equipment can carry multiple miniaturized deep-sea soft robotic fish to work together in deep-sea operations, providing more possibilities for efficient and intelligent deep-sea exploration," Professor Guorui Li introduced.
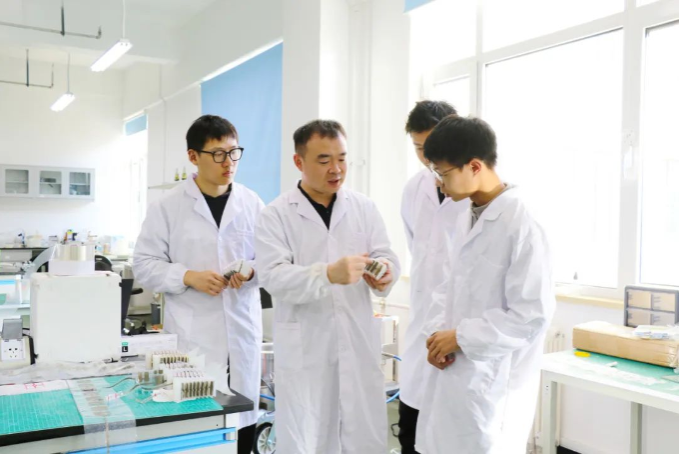
Professor Guorui Li guiding students
In 2021, under the guidance of Professor Tie Feng Li from Zhejiang University, Guorui Li, as the first author, published a cover article in the journal Nature titled "Self-powered soft robot in the Mariana Trench," designing a deep-sea soft robot fish measuring 22 centimeters in length and 28 centimeters in wingspan. This research pioneered the pressure adaptation theory and systematic design methods for soft robots in the hadal zone, achieving for the first time the propulsion of a soft robot without a pressure vessel at 10,900 meters in the Mariana Trench and autonomous navigation at 3,224 meters in the South China Sea. This achievement was selected as one of the "Top Ten Scientific Progressions in China" for the year 2021.
In April 2022, Guorui Li returned to his alma mater, Harbin Engineering University, to establish the Soft Underwater Robotics Laboratory, focusing on the cutting-edge direction of "soft robots and flexible intelligent systems in extreme underwater environments." The laboratory conducts interdisciplinary research on fundamental theories, device design, and system integration of soft robots and flexible intelligent systems under extreme loads such as deep-sea environments and underwater explosions. It aims to develop systematic design theories, system integration, and application methods for underwater soft robot systems, providing new breakthroughs for future research on highly adaptive underwater intelligent equipment.
Source link:https://www.nature.com/articles/s41467-023-42882-3